Con desperdicios alimentarios, polímeros e impresión 3D, investigadores del proyecto europeo BARBARA han fabricado embellecedores de puertas y frentes de salpicadero para vehículos, así como uniones para vigas. Entre sus ‘ingredientes’ figuran polisacáridos del maíz, aditivos de granada y fragancias de limón con cáscara de almendra.
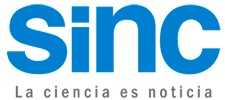
Cuatro años después de su inicio, los investigadores del proyecto europeo BARBARA han finalizado la creación de nuevos materiales a partir de desperdicios alimentarios, con los que se han fabricado prototipos para los sectores de la automoción y la construcción. Esta semana se han presentado en la sede de Aitiip-Centro Tecnológico en Zaragoza, desde donde se ha coordinado esta iniciativa.
Con la ayuda de una tecnología denominada deposición de filamento fundido (FFF, por sus siglas en inglés: fused filament fabrication), la más extendida para la impresión 3D o fabricación aditiva, se han obtenido piezas innovadoras con aplicación industrial.
Usando desperdicios alimentarios e impresión 3D, se han fabricado embellecedores de puertas y frentes de salpicaderos para vehículos, así como uniones para vigas y otras estructuras empleadas en la construcción
En concreto, se han desarrollado embellecedores de puertas de automóviles, frentes de salpicaderos, moldes y utillajes para fabricar nudos para y celosías de vigas y estructuras como las que se utilizan en construcción. Estas piezas se procesaron a partir de ocho nuevos materiales con los que se fabricaron varias bobinas de filamento adecuadas para la impresión en 3D.
Los materiales contienen como polímeros principales poliéster y poliamida mezclados con polisacáridos obtenidos del maíz, así como aditivos procedentes de la granada, pigmento y fragancia de limón y cáscara de almendra, que confieren a los materiales diferentes colores, fragancias y texturas con propiedades antimicrobianas y antioxidantes.
Economía circular
Aunque de momento son prototipos, la idea de sus creadores es obtener piezas finales de gran calidad que comienzan a ser una realidad en el vehículo eléctrico, así como los moldes y utillajes que cada vez se utilizan más dentro de una fabricación híbrida en el marco del sector europeo de la bioeconomía y la economía circular.
Pieza para el salpicadero de un coche fabricada con esta técnica. / AITIIP
El proyecto BARBARA (Biopolymers with advanced functionalities for building and automotive parts processed through additive manufacturing) ha contado con un presupuesto de 2,7 millones de euros, de los que la Comisión Europea, a través del Biobased Bioindustries Joint Undertaking (BBI), ha aportado una gran parte.
Colaboración de empresas y universidades
Han participado 10 socios de España, Italia, Suecia y Bélgica. Aitiip-Centro Tecnológico ha sido el responsable del desarrollo del nuevo proceso de impresión 3D y de la fabricación de los prototipos.
En cuanto al resto de los socios, FECOAM ha sido el proveedor de desperdicios alimentarios; Celabor, KTH y la Universidad de Alicante han desarrollado los procesos químicos de extracción de las moléculas funcionales y polisacáridos; Nurel ha sido el proveedor de los biopolímeros comerciales; la Universidad Italiana di Perugia ha desarrollado el material a nivel de laboratorio y Tecnopackaging a nivel piloto, además de fabricar las bobinas de material para impresión; y Acciona Construcción y Centro Ricerche FIAT han sido los socios industriales encargados de validar los prototipos.
Fuente: Aitiip-Centro Tecnológico
Derechos: Creative Commons.
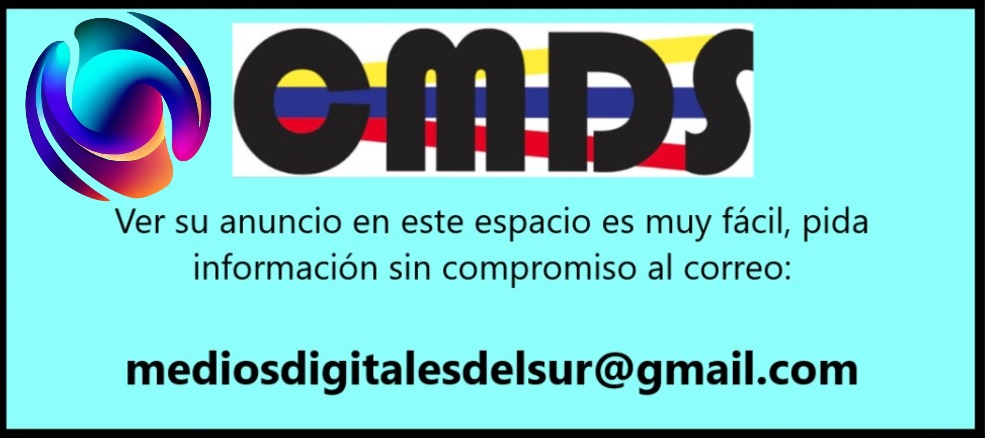